Injection Molding: A Precision Tool for Medical Device Manufacturing
Injection molding is a versatile manufacturing process that has found widespread application in the medical device industry.
Share this Post to earn Money ( Upto ₹100 per 1000 Views )
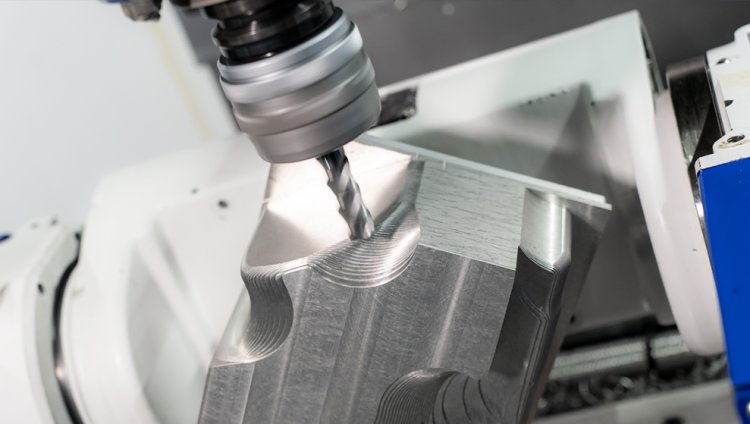
Injection molding is a versatile manufacturing process that has found widespread application in the medical device industry. This technique involves injecting molten plastic into a mold cavity, where it cools and solidifies to form the desired shape. From simple components to complex assemblies, injection molding offers a range of benefits that make it an ideal choice for medical device manufacturers.
Precision and Efficiency
One of the key advantages of injection molding is its ability to produce parts with exceptional precision and accuracy. This is essential for medical devices, which must meet stringent quality standards to ensure patient safety and effectiveness. Additionally, injection molding is a highly efficient process that can produce large quantities of parts in a relatively short amount of time.
Versatility and Material Options
Injection molding is a versatile process that can be used with a wide range of plastic materials, including biocompatible options that are suitable for medical applications. This flexibility allows manufacturers to select the most appropriate material for their specific needs, ensuring that the medical device meets the required performance characteristics.
The Molding Process
The injection molding process typically involves the following steps:
- Mold Design and Fabrication: A mold is designed to create the desired shape of the medical device component. The mold is then fabricated using a variety of materials, such as steel or aluminum.
- Material Preparation: The plastic material is heated and melted to a liquid state.
- Injection: The molten plastic is injected into the mold cavity under high pressure.
- Cooling: The plastic cools and solidifies within the mold cavity.
- Ejection: The finished part is ejected from the mold.
Key Considerations
- Material Selection: Choosing the right plastic material is crucial for ensuring the biocompatibility, durability, and performance of medical devices.
- Mold Design: The design of the injection mold must be optimized for efficient production and to prevent defects such as flash or sink marks.
- Molding Parameters: Factors such as injection pressure, temperature, and cooling time must be carefully controlled to achieve the desired part quality.
- Quality Control: Rigorous quality control measures are essential to ensure that medical devices meet regulatory requirements and are safe for use.
RPWORLD: Your Partner in Medical Device Manufacturing
At RPWORLD, we specialize in providing comprehensive injection molding solutions for the medical device industry. Our team of experts can assist with:
- Mold Design and Fabrication: We have the capabilities to design and fabricate high-quality injection molds that meet the specific needs of your medical device application.
- Material Selection: Our engineers can help you choose the most appropriate plastic material for your medical device components.
- Process Optimization: We can optimize the injection molding process to ensure efficient production and high-quality parts.
- Quality Assurance: We implement rigorous quality control measures to ensure that your medical devices meet all regulatory requirements.
Conclusion
Injection molding is a powerful tool for manufacturing medical devices, offering precision, efficiency, and versatility. By partnering with RPWORLD, you can leverage our expertise in injection molding to bring your medical device ideas to life and meet the demanding requirements of the healthcare industry.