Addressing Challenges in Reactive Ion Etching Systems: Strategies and Solutions
Reactive Ion Etching Systems play a pivotal role in the field of Thin Film Technology, enabling the precise fabrication of intricate patterns and structures on various substrates.
Share this Post to earn Money ( Upto ₹100 per 1000 Views )
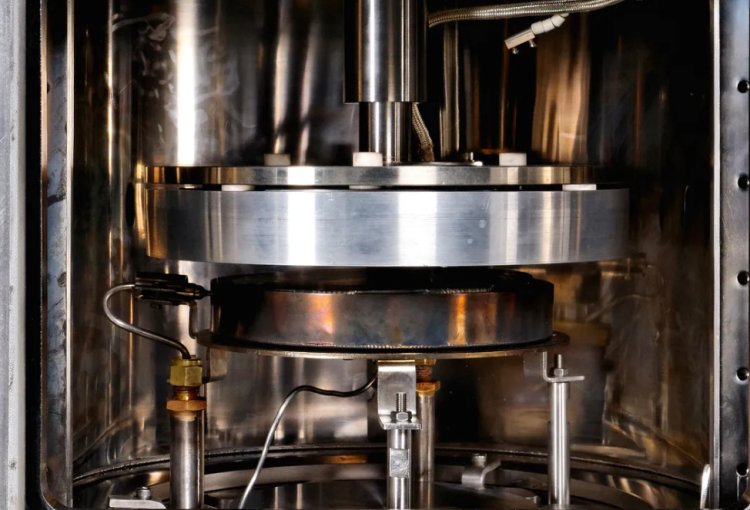
Reactive Ion Etching Systems play a pivotal role in the field of Thin Film Technology, enabling the precise fabrication of intricate patterns and structures on various substrates. However, like any sophisticated technology, Reactive Ion Etching Systems encounter challenges that can hinder efficiency and quality. In this article, we delve into these challenges and explore strategies and solutions to overcome them.
One common challenge in Reactive Ion Etching Systems is achieving uniform etching across large substrate areas. Variations in gas flow, temperature, and pressure can lead to non-uniformity, affecting the quality and consistency of the etched features. To address this, precise control mechanisms and real-time monitoring systems are essential. Implementing feedback control loops can help adjust parameters dynamically, ensuring uniform etching across the substrate.
Another significant challenge is etch selectivity, especially when dealing with complex material stacks. Thin film technology often involves etching multiple layers with different compositions and properties. Achieving high selectivity between layers is crucial to avoid damage to underlying structures. Advanced gas chemistry and process optimization techniques can enhance selectivity, allowing for precise control over etch rates and material removal.
Contamination is another issue that plagues Reactive Ion Etching Systems, particularly in high-volume manufacturing environments. Residual gases, particles, and by-products can accumulate over time, leading to process drift and reduced performance. Regular maintenance protocols, including chamber cleaning and purging procedures, are essential to mitigate contamination risks and maintain system integrity.
Moreover, achieving high aspect ratio features poses a significant challenge in Reactive Ion Etching Systems. As feature sizes shrink and aspect ratios increase, the etching process becomes more complex. Addressing this challenge requires innovative process designs and optimized plasma parameters to ensure sidewall passivation and prevent feature collapse.
Furthermore, Reactive Ion Etching Systems face challenges related to etch uniformity and repeatability across different substrate materials. Variations in material properties such as composition, crystallinity, and surface roughness can affect etch rates and selectivity. Developing customized process recipes and material-specific etch chemistries can help overcome these challenges, ensuring consistent results across diverse substrate types.
In conclusion, while Reactive Ion Etching Systems offer unparalleled capabilities in Thin Film Technology, they are not without their challenges. By implementing advanced control strategies, optimizing process parameters, and embracing innovative solutions, these challenges can be effectively addressed, unlocking the full potential of Reactive Ion Etching Systems in modern semiconductor and microfabrication industries.
Contact Us
For more information, Visit: https://hhvadvancedtech.com/
Site No. 17, Phase 1, Peenya Industrial Area, Bengaluru – 560058, India
Phone: +91-80-66703700
Fax: +91-80-66703800
Email: infotfed@hhvadvancedtech.com