What is a fiber welder and how does it revolutionize the metal welding industry with its technology and advantages
A fiber welder, also known as a fiber laser welding machine, is a high-tech welding system that uses a fiber laser as its energy source to join metal components.
Share this Post to earn Money ( Upto ₹100 per 1000 Views )
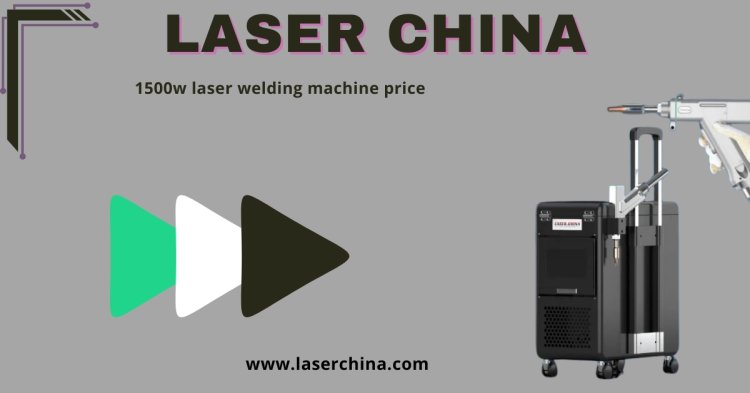
A fiber welder, also known as a fiber laser welding machine, is a high-tech welding system that uses a fiber laser as its energy source to join metal components. This type of laser welding has become increasingly popular in the manufacturing and fabrication industries due to its speed, precision, efficiency, and ability to weld a wide variety of metals with minimal heat distortion.
What is Fiber Laser Welding?
Fiber laser welding works by focusing a high-powered laser beam (transmitted through an optical fiber) onto the material to melt and fuse it together. Unlike traditional arc welding methods that rely on an electric arc and filler materials, fiber welding creates extremely focused heat zones, allowing for deep penetration with narrow seams and very little thermal impact on surrounding areas.
Fiber lasers are powered by diodes and use optical fibers to amplify and deliver the beam, making them compact, efficient, and capable of producing consistent energy output.
Key Features of Fiber Welders
-
High Beam Quality: Fiber lasers provide an extremely fine and stable beam that enables ultra-precise welding, especially useful for thin or delicate metals.
-
Energy Efficiency: These machines are far more energy-efficient compared to traditional CO₂ lasers or arc welding methods, which leads to cost savings in power consumption.
-
Long Lifespan: Fiber lasers have fewer moving parts and a sealed design, offering long operational lifespans with low maintenance requirements.
-
Speed: Fiber welders are significantly faster than conventional welding methods. For high-volume production, this leads to higher output and lower labor costs.
Benefits of Fiber Welders in the Industry
-
Superior Weld Quality:
The focused beam creates narrow, deep welds with minimal distortion and oxidation. This results in cleaner and stronger joints with a smooth finish, often requiring no post-weld grinding or polishing. -
Minimal Heat-Affected Zone (HAZ):
Because the laser beam is so precise, it minimizes the amount of heat applied to the surrounding material. This preserves the structural integrity of the metal and is particularly advantageous when welding heat-sensitive or thin materials. -
Versatility in Materials:
Fiber welders can weld a wide range of metals, including carbon steel, stainless steel, aluminum, brass, copper, titanium, and more. This makes them ideal for industries like automotive, aerospace, electronics, medical device manufacturing, and jewelry. -
Automation-Friendly:
Fiber welders can be easily integrated into robotic arms and CNC systems, enabling full automation of the welding process. This is essential for modern, high-precision manufacturing environments. -
Low Operating Costs:
With minimal consumables, no need for filler wire in many applications, and low maintenance, fiber welders offer cost-effective long-term solutions for businesses.
Applications of Fiber Welders
Fiber welders are widely used in:
-
Automotive part manufacturing
-
Precision instrument assembly
-
Sheet metal fabrication
-
Medical device welding
-
Electronics and battery component welding
Conclusion
The fiber welder is redefining how metal components are joined in the modern industrial landscape. Its unmatched precision, speed, and efficiency make it a valuable tool for any manufacturer seeking to improve productivity and product quality. As industries continue to shift toward automation and high-performance solutions, fiber welding will play an even more critical role in shaping the future of metal fabrication. Whether for large-scale production or precision micro-welding, fiber welders are a smart investment for advanced manufacturing needs.