What are the key benefits and challenges of using laser welding for stainless steel applications
Laser welding is increasingly used in industries that require high precision and quality, especially when working with materials like stainless steel.
Share this Post to earn Money ( Upto ₹100 per 1000 Views )
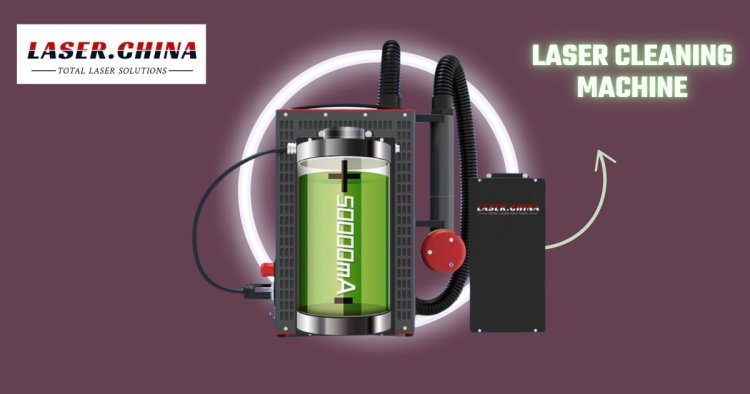
Laser welding is increasingly used in industries that require high precision and quality, especially when working with materials like stainless steel. Known for its accuracy and efficiency, laser welding has several advantages, but it also presents certain challenges that need to be considered. Understanding both the benefits and the challenges is crucial for businesses that wish to incorporate this advanced welding technique into their manufacturing processes.
Benefits of Laser Welding for Stainless Steel
-
High Precision and Control: One of the primary advantages of laser welding, particularly for stainless steel, is the precision it offers. The laser beam can be focused into a very small spot, which allows for detailed and accurate welds, even in intricate or thin-walled stainless steel components. This precision ensures minimal distortion and reduces the likelihood of defects, which is vital for industries such as electronics, aerospace, and medical device manufacturing.
-
Minimal Heat-Affected Zone (HAZ): Laser welding produces a highly focused energy source that is capable of welding without generating excessive heat. As a result, the heat-affected zone (HAZ)—the area of the stainless steel that is affected by the heat from the weld—remains small. This is critical for maintaining the integrity of the material, as stainless steel can lose its corrosion resistance or become weakened if the HAZ is too large. The reduced heat input also minimizes warping and distortion of the workpiece.
-
Faster Welding Speeds: Laser welding is a high-speed process, allowing manufacturers to increase production rates while maintaining quality. Compared to traditional welding techniques, laser welding can produce faster welds with greater consistency, which is particularly advantageous when working with stainless steel in large quantities or on time-sensitive projects.
-
Minimal Post-Welding Treatment: Due to the high precision and controlled heat input, laser welding generally results in a smooth, high-quality weld. This reduces the need for extensive post-weld cleaning, finishing, or grinding, which can be time-consuming and costly. In applications that require a clean and aesthetically appealing finish, such as in the food industry or medical devices, laser welding is an ideal solution.
-
Ability to Weld Complex Shapes: Laser welding is particularly effective for welding complex geometries and hard-to-reach areas. This is important when dealing with stainless steel parts that have intricate shapes or require multi-angle welding. The laser beam’s ability to be directed precisely to the welding location allows for easy integration into automated systems for such specialized tasks.
-
Low Energy Consumption: While the initial investment in a laser welding machine may be higher, the process itself typically requires less energy than traditional welding methods. This is due to the focused nature of the laser beam, which targets only the material to be welded, resulting in reduced energy usage.
Challenges of Laser Welding for Stainless Steel
-
High Initial Equipment Cost: One of the major challenges with laser welding is the high cost of the equipment. Laser welding machines, particularly those that are high-powered and capable of welding thicker stainless steel, can be expensive. For smaller businesses or those with limited budgets, this upfront investment can be a significant barrier.
-
Thickness Limitations: While laser welding excels with thin materials, welding thicker stainless steel components can present difficulties. For thicker sections, additional passes or higher-powered lasers may be required to achieve full penetration. Even with adjustments, it can be challenging to achieve a uniform weld in thicker materials, making laser welding more suitable for thin to medium thickness materials unless high-powered systems are used.
-
Sensitivity to Surface Contaminants: Stainless steel can be sensitive to contaminants such as oil, rust, and dirt. Since laser welding relies on a precise, focused beam, any contaminants on the surface of the material can interfere with the quality of the weld. Cleaning the surface thoroughly before welding is essential to ensure the desired results, adding an extra step to the process.
-
Operator Skill Requirements: Although laser welding systems can be automated, they still require highly skilled operators to ensure proper machine setup, calibration, and parameter adjustment. Factors such as laser power, beam focus, and welding speed need to be optimized for each stainless steel application. Incorrect settings can lead to poor-quality welds, including porosity, weak joints, or excessive heat input.
-
Limited Mobility for Certain Applications: While laser welding is highly effective in a controlled, stationary environment, its application for mobile or field welding is more limited. The equipment can be bulky, and setting up laser systems for portable use is not as straightforward as traditional methods like TIG or MIG welding, which can be more easily moved to job sites.
-
Maintenance and Component Wear: Laser welding systems, particularly high-powered lasers, require regular maintenance to ensure optimal performance. The components of the laser system, such as lenses, mirrors, and the laser itself, can wear out over time and may need replacement. This can increase the cost of maintaining a laser welding setup, making it a consideration for businesses weighing the long-term costs.
Conclusion
Laser welding is a powerful technique for welding stainless steel, offering significant advantages such as high precision, speed, minimal distortion, and the ability to weld complex geometries. These benefits make it a valuable option for industries that demand high-quality, consistent welds. However, the high initial investment, challenges with thicker materials, sensitivity to surface contaminants, and maintenance requirements are important considerations. By understanding both the advantages and the challenges of laser welding, companies can make more informed decisions about whether this technology is the right fit for their specific applications.