What are Pneumatic Cylinders and Actuators?
Discover what pneumatic cylinders and actuators are, how they work, and their industrial uses with Hikari Automation Systems Pte Ltd.
Share this Post to earn Money ( Upto ₹100 per 1000 Views )
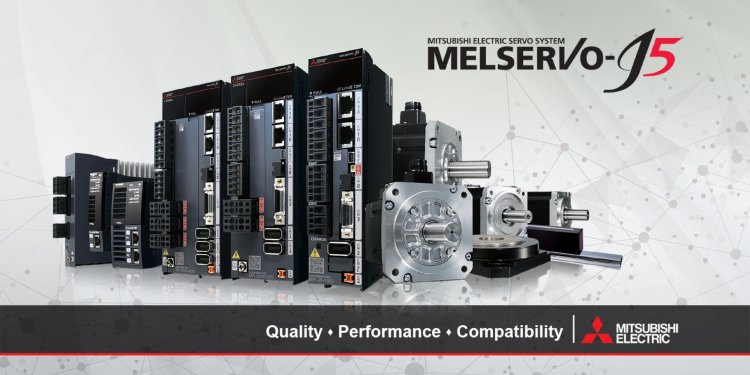
Definition and Purpose
Pneumatic cylinders and actuators are fundamental components in many modern industrial automation systems. Powered by compressed air, they serve as mechanical devices designed to produce motion or force. In simpler terms, they help machines "move" — whether it’s lifting, pushing, pulling, rotating, or clamping — using air as the driving medium. This is a major advantage in environments where cleanliness, speed, and safety are crucial.
These devices are widely used in various sectors, from packaging and food production to automotive assembly and material handling. For companies like Hikari Automation Systems Pte Ltd, pneumatic solutions form the backbone of their smart automation designs. As a company specializing in advanced automation systems, they leverage pneumatic cylinders and actuators for precision, reliability, and cost-efficiency.
But why air? Compressed air is abundant, safe, and easy to control. This makes pneumatic devices extremely versatile and attractive for operations requiring consistent mechanical motion. Unlike hydraulic systems that depend on fluid power or electric actuators that rely on electrical motors, pneumatic actuators and cylinders combine clean energy with mechanical output.
Understanding these tools is essential for grasping how automation systems can function seamlessly in manufacturing lines or robotic arms.
Brief History and Evolution in Automation
The roots of pneumatic systems trace back to ancient civilizations that used wind power for various applications like water transport and basic machinery. But the true industrial use of pneumatics started in the 19th century during the industrial revolution, with the advent of air compressors and steam engines.
Over the decades, pneumatic technologies evolved rapidly. By the mid-20th century, industries began to adopt pneumatic automation in full force, especially in sectors demanding fast and repetitive motion. The appeal of air-powered tools became evident — they were cleaner than oil-powered hydraulics, faster than manual labor, and often cheaper than electric alternatives.
Today, companies like Hikari Automation Systems continue to push the envelope. With the integration of sensors, IoT, and PLCs (Programmable Logic Controllers), pneumatic systems are now smarter than ever. They’re capable of self-monitoring, adapting in real-time, and reducing downtime — all while ensuring energy efficiency.
Understanding the Basics of Pneumatic Systems
What is a Pneumatic System?
At its core, a pneumatic system is a mechanical setup that uses compressed air to generate controlled motion. Think of it like a lung for machines — when compressed air is released into the system, it moves the internal parts (like pistons or gears), which then perform mechanical work.
A standard pneumatic system is composed of three main stages:
-
Air Generation – Using compressors to generate compressed air.
-
Air Conditioning – Filtering, regulating, and lubricating the air before use.
-
Air Distribution – Transporting the air through valves and tubing to the actuators or cylinders.
This closed-loop system can power multiple devices simultaneously, and is especially effective in tasks where repetitive motion or light-to-medium force is required.
Components of a Pneumatic System
Let’s break down the essential parts of a typical pneumatic system:
-
Compressor: Creates and stores compressed air.
-
FRL Unit (Filter, Regulator, Lubricator): Prepares the air for smooth operation.
-
Valves: Control airflow direction, pressure, and timing.
-
Actuators (or Cylinders): Convert air pressure into mechanical motion.
-
Tubing & Connectors: Distribute air from the source to the end components.
Each component must work in harmony to maintain system efficiency. A blockage in the tubing or faulty regulator can cripple the entire setup, which is why maintenance and high-quality components — like those provided by Hikari Automation Systems — are essential.
What Are Pneumatic Cylinders?
Pneumatic Cylinder Explained
A pneumatic cylinder, also called an air cylinder, is a mechanical device that uses compressed air to produce a linear or rotary motion. When air enters one side of the cylinder, it pushes a piston to the other side, thereby generating mechanical force and motion.
These cylinders are the “muscles” of a pneumatic system. They can be used to lift, press, rotate, or clamp objects with ease. Depending on the application, pneumatic cylinders come in different sizes, force capacities, and mounting configurations.
Hikari Automation Systems designs and integrates these cylinders into custom solutions across various industries. Their cylinders offer high durability, consistent performance, and minimal maintenance.
Working Principle of Pneumatic Cylinders
The operation of a pneumatic cylinder is based on Pascal’s Law, which states that pressure applied to a confined fluid is transmitted equally in all directions. In the case of pneumatics, the fluid is compressed air.
Here’s a simplified version of how it works:
-
Air Intake: Compressed air is directed into the cylinder chamber.
-
Piston Movement: The pressure pushes the piston inside the cylinder.
-
Mechanical Work: The piston’s movement creates linear force and motion.
-
Exhaust: Once the work is done, the air exits the chamber via an exhaust port.
Depending on the design, cylinders may work with one or both sides of the piston:
-
Single-acting cylinders use air pressure to move in one direction and a spring to return.
-
Double-acting cylinders use air pressure in both directions, providing greater control and force.
Types of Pneumatic Cylinders
There are several types of pneumatic cylinders, each tailored for specific applications:
-
Single-Acting Cylinders (SAC): Simple design, uses a spring for return stroke.
-
Double-Acting Cylinders (DAC): Uses air pressure for both extend and retract strokes.
-
Telescopic Cylinders: Multi-stage pistons allow for longer strokes in compact spaces.
-
Rotary Cylinders: Produces rotary motion instead of linear.
-
Rodless Cylinders: No external rod; ideal for limited space and long strokes.
-
Compact Cylinders: Short strokes, space-saving design.
These variations ensure that automation engineers have the flexibility to select the right cylinder for every specific task.
What Are Pneumatic Actuators?
Pneumatic Actuator Overview
A pneumatic actuator is a device that transforms compressed air energy into mechanical motion — either linear or rotary. While pneumatic cylinders are technically a type of actuator, the term “actuator” broadly encompasses any air-powered device that performs mechanical work.
Actuators can be found in everything from conveyor belt pushers to automated door openers. They are known for their responsiveness, reliability, and energy efficiency. When integrated into industrial setups by experts like Hikari Automation Systems, actuators help streamline production processes, reduce human error, and improve output speed.
Different Types of Pneumatic Actuators
Pneumatic actuators come in several forms based on the type of motion and control needed:
-
Linear Actuators: Include standard air cylinders, rodless cylinders, and guided actuators.
-
Rotary Actuators: Convert air pressure into rotary motion. Useful in valve control and turntables.
-
Gripper Actuators: Used in robotics to hold or manipulate objects.
-
Diaphragm Actuators: Used for precision applications like valve positioning.
Each type has unique advantages, depending on the specific task — whether it's speed, torque, size, or control precision.
Key Applications in Industrial Automation
Pneumatic actuators play a crucial role in automating repetitive tasks. Common applications include:
-
Material handling systems
-
Packaging and labeling lines
-
Pick and place robots
-
Food processing machinery
-
Automotive assembly lines
In all these scenarios, the aim is the same — improve speed, accuracy, and safety while reducing labor costs and system downtimes.
Conclusion:
Pneumatic cylinders and actuators play a pivotal role in modern automation, offering a cost-effective, reliable, and clean solution for a wide array of industrial applications. Whether it's for packaging, assembly, automotive, or even food processing, these air-powered components deliver consistent performance with minimal maintenance. Hikari Automation Systems Pte Ltd understands the critical importance of precision and efficiency in industrial automation, which is why they offer cutting-edge pneumatic solutions tailored to meet your specific needs.