Vacuum Brazed Cold Plates: The Secret to Superior Liquid Cooling Efficiency!
A vacuum brazed cold plate is a high-performance liquid cooling component used in thermal management systems. It is manufactured using vacuum brazing, a process that fuses metal components together in a controlled vacuum environment, ensuring leak-free, high-strength joints with excellent thermal conductivity. These cold plates efficiently dissipate heat from electronic components, batteries, and power devices by circulating coolant through internal channels. Commonly made from aluminum or copper, vacuum brazed cold plates are widely used in industries like aerospace, electric vehicles, and high-power electronics for reliable and efficient cooling.
Share this Post to earn Money ( Upto ₹100 per 1000 Views )
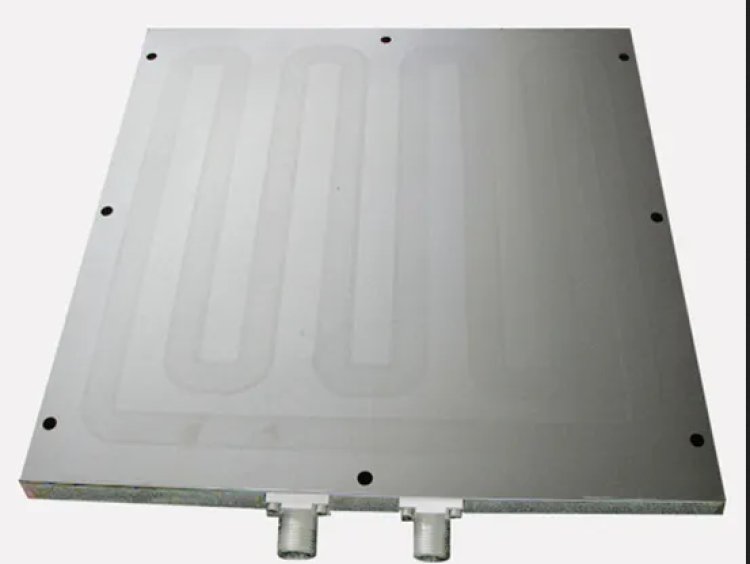
As technology continues to evolve, so do the thermal management challenges faced by industries relying on high-performance electronics. From data centers and electric vehicles to aerospace systems and power electronics, efficient cooling is crucial to maintaining optimal performance, energy efficiency, and system reliability.
Traditional cooling methods, such as air cooling and basic heat sinks, struggle to keep up with the increasing power densities of modern electronics. This is where vacuum brazed cold plate technology emerges as a game-changer, offering superior thermal efficiency, enhanced durability, and compact design.
A vacuum brazed cold plate is a specialized liquid cooling solution designed for efficient heat dissipation in high-power applications. By utilizing vacuum brazing, this technology ensures a strong, leak-proof, and highly conductive cooling system capable of handling extreme thermal loads.
What Is a Vacuum Brazed Cold Plate?
Understanding Cold Plate Cooling
A cold plate is a liquid-cooled heat transfer device used to efficiently remove heat from high-power components such as CPUs, GPUs, batteries, and power electronics. Instead of relying on air cooling, which has limited effectiveness in high-performance systems, cold plates circulate a cooling liquid (such as water or glycol) to absorb and dissipate heat more effectively.
The Role of Vacuum Brazing in Cold Plate Design
Vacuum brazing is a high-temperature joining process that fuses multiple layers of metal together without the need for welds or fasteners. This creates:
- A seamless, leak-proof cooling system
- Enhanced thermal conductivity
- A lightweight and compact design
Unlike other cold plate manufacturing techniques, vacuum brazed cold plates eliminate the need for tubing, allowing for more intricate and efficient liquid flow paths.
Why Vacuum Brazed Cold Plates Outperform Other Cooling Methods
- Exceptional Thermal Conductivity
By eliminating air gaps and ensuring maximum metal-to-metal contact, vacuum brazed cold plates offer unparalleled heat transfer efficiency.
- Enhanced Structural Integrity and Leak Prevention
The brazing process creates a single, solid structure, eliminating weak points where leaks or failures could occur.
- Lightweight and Compact Design for Space-Constrained Applications
Since vacuum brazing allows for integrated cooling channels without tubing, the result is a slimmer and more lightweight design perfect for compact electronic systems.
- High Reliability for Demanding Environments
From aerospace to industrial automation, vacuum brazed cold plates provide high-performance cooling even in extreme conditions.
Applications of Vacuum Brazed Cold Plates
Data Centers and High-Performance Computing (HPC)
- Keeps processors and power modules cool under extreme workloads.
- Enhances energy efficiency and prevents downtime.
Electric Vehicles (EVs) and Battery Cooling
- Essential for maintaining battery temperature stability.
- Helps improve EV battery lifespan and efficiency.
Aerospace and Defense Thermal Management
- Ensures critical components remain operational under high-stress conditions.
- Reduces weight while maximizing cooling performance.
Power Electronics and Renewable Energy Systems
- Essential for thermal regulation in power inverters and energy storage systems.
- Improves the efficiency of high-voltage power converters.
How Tone Cooling Technology Co., Ltd. Excels in Vacuum Brazed Cold Plate Manufacturing
At Tone Cooling Technology Co., Ltd., we specialize in high-precision vacuum brazed cold plates tailored for aerospace, EVs, data centers, and high-power electronics. Our state-of-the-art manufacturing processes and strict quality controls ensure superior performance in thermal management solutions.
Vacuum brazed cold plates are the future of high-performance liquid cooling, offering exceptional thermal efficiency, durability, and design flexibility. Whether in data centers, electric vehicles, or industrial power systems, these advanced cooling solutions provide superior performance and reliability.
With Tone Cooling Technology Co., Ltd., industries gain access to custom-engineered cooling solutions designed to meet the most demanding thermal challenges.
FAQs
1. What makes vacuum brazed cold plates different from standard cold plates?
Vacuum brazed cold plates are manufactured using a high-temperature brazing process that fuses metal layers together without welds or fasteners. This results in a seamless, leak-proof structure with enhanced thermal conductivity and superior heat dissipation compared to traditional cold plates that rely on embedded tubing or mechanical joining methods.
2. Are vacuum brazed cold plates suitable for high-power electronics?
Yes! Vacuum brazed cold plates are ideal for high-power electronics such as data center processors, power inverters, electric vehicle batteries, and aerospace components. They provide efficient cooling and help maintain stable operating temperatures, preventing thermal damage and performance loss.
3. How durable are vacuum brazed cold plates?
Vacuum brazed cold plates are highly durable due to their seamless construction. The brazing process eliminates weak points, making them resistant to leaks, corrosion, and mechanical stress. They are designed to withstand harsh environments such as extreme temperatures and high-pressure conditions.
4. Can vacuum brazed cold plates be customized for specific applications?
Absolutely! Tone Cooling Technology Co., Ltd. specializes in custom-engineered vacuum brazed cold plates tailored to specific industry needs. Design features such as custom cooling channels, size variations, and optimized thermal performance can be adjusted to meet unique cooling requirements.
5. What industries benefit the most from vacuum brazed cold plate technology?
Vacuum brazed cold plates are widely used in:
- Data Centers & High-Performance Computing (HPC) – Cooling for CPUs, GPUs, and high-power servers.
- Electric Vehicles (EVs) & Battery Cooling – Maintaining optimal battery temperature stability for longer lifespan and efficiency.
- Aerospace & Defense – Thermal management for avionics, satellites, and high-precision military electronics.
- Power Electronics & Renewable Energy – Cooling for power inverters, industrial transformers, and energy storage systems.