The Ultimate Guide to Sheet Metal Punching in Precision Manufacturing
Explore the ultimate guide to sheet metal punching in precision manufacturing. Learn about techniques, tools, and benefits to optimize your production process.
Share this Post to earn Money ( Upto ₹100 per 1000 Views )
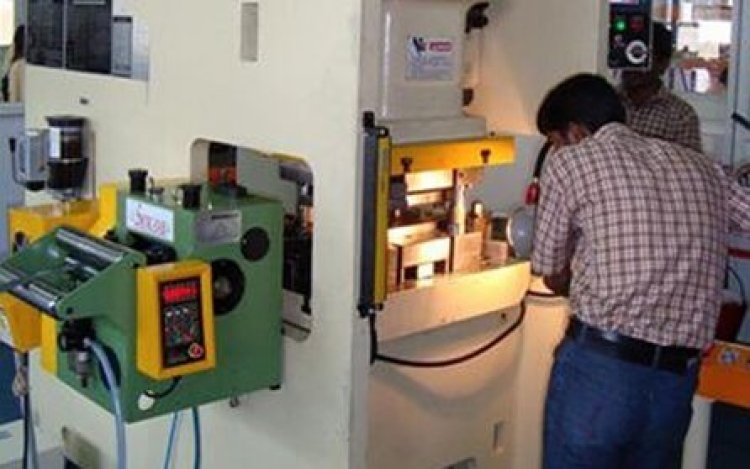
Sheet metal punching is an important step of precision sheet metal fabrication that assists in achieving many types of finished as well as semi-finished products. In this process, a sheet metal punch tool applies pressure on the metal surface in order to design. It plays a significant role in the automotive, electronics, and other industries because it makes precise holes, shapes, and patterns possible. To know more about this process, continue to read this ultimate guide:
What Are the Working Procedures for Sheet Metal Punching?
The sheet metal punching process may appear simple, but it requires numerous stages to ensure precision and efficiency. Here's how it normally works:
-
Step 1: Material Selection
First, a suitable metal sheet is chosen depending on the project specifications. This covers consideration for metal kind, thickness, and characteristics.
-
Step 2: Design and Plan
Engineers and designers create detailed designs and layouts for the punching process. This involves designing the punchable components as well as arranging the punches and dies.
-
Step 3: Setup the Punch Press
To set up the sheet metal punch press, insert the suitable die and punch set into the machine. Achieving precision in punching wants careful alignment and accurate positioning.
-
Step 4: Programming
Programming is required for CNC turret punches and other automated equipment. This stage involves entering the design parameters into the machine's computer, which regulates the movement and activity of the punches.
-
Step 5: Sheet Placement
In the next step the metal sheet is tightly attached to the machine bed in order to avoid any movement at the time of punching process.
-
Step 6: Punching
The machine starts, and the punch presses the metal sheet into the die and it forms shapes or holes. The Precision punching tools speed and force is adjusted to protect the metal.
-
Step 7: Post-processing
To improve look and functionality, punched parts must go through further processing, such as deburring, cleaning, and secondary finishing.
Materials and Capabilities of Sheet Metal Punching
-
Materials suitable for punching
Sheet metal hole punching is the most generally used technique in manufacturing components within various industries since it can work on various materials including steel, aluminum, copper, and other alloys. This process is widely used by automotive metal stamping companies to create durable components.
-
Range of Capabilities
Sheet metal punching is a flexible and strong process that can withstand varied material thicknesses, hole sizes, and complex geometries to suit various designs.
-
Expert punching
The capacity of sheet metal punch tools to effectively process steel, aluminum, copper, and alloys emphasizes its importance in meeting the fabrication needs of diverse industrial sectors.
The Bottom Line
Punching sheet metal is the fundamental process in precision sheet metal fabrication. It is accurate and efficient in producing a wide variety of products in metal components. Hence, as technology advances with time, the role for sheet metal punching will naturally grow with new innovations and maintain its importance in modern times. Thus, choosing Custom punch press services for your business is the right choice. It helps you to get high-quality, tailored results that improve efficiency and allow you to stay ahead of the competition in today's rapidly evolving market.