The Power of Precision: Why The Right Tools and Parts Matter
The Power of Precision: Why The Right Tools and Parts Matter. Read to find out more!
Share this Post to earn Money ( Upto ₹100 per 1000 Views )
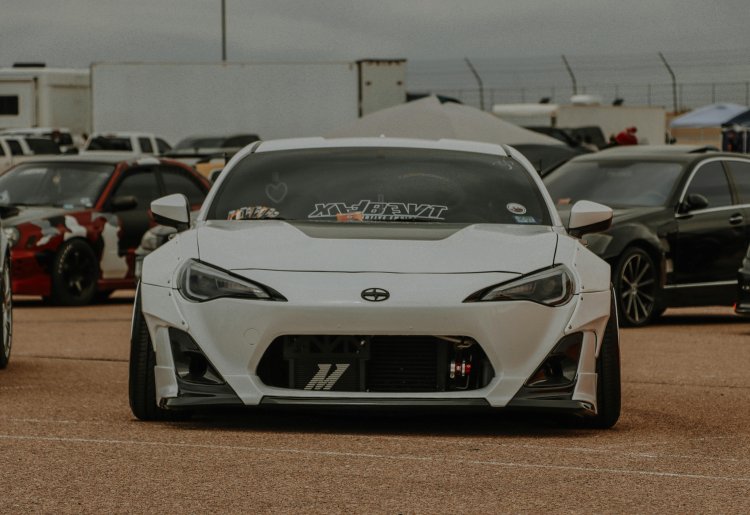
When it comes to the intricacies of mechanical engineering and automotive performance, precision is not just a buzzword—it is the fundamental difference between mediocrity and excellence. From the smallest air intake component to the most complex industrial machinery, the quality of tools and parts can make or break an entire system's performance, efficiency, and longevity.
Every engineer, mechanic, and craftsperson understands that the foundation of superior work lies in the meticulous selection of components and tools. This commitment to precision transcends mere technical specifications; it represents a philosophy of excellence that permeates every aspect of design, manufacturing, and maintenance.
The Anatomy of Precision
Precision is more than just accuracy—it is about understanding the delicate interplay between various components and how they interact to create a seamless, high-performing system. Consider an automotive engine, where each part must work in near-perfect harmony. A misaligned component, a substandard part, or an improperly designed system can lead to catastrophic failures, reduced performance, and significantly increased wear and tear.
Take, for example, the exhaust system of a high-performance vehicle. It is not merely a conduit for expelling combustion gases; it is a complex engineering marvel that impacts engine efficiency, sound, and overall vehicle performance. The right exhaust system can enhance horsepower, improve fuel economy, and even contribute to the vehicle's acoustic signature.
The Hidden Costs of Compromise
Many individuals and organisations are tempted to cut corners by selecting cheaper, lower-quality parts. While the initial cost savings might seem attractive, the long-term consequences can be devastating. Inferior components often lead to:
· Increased maintenance costs.
· Reduced system reliability.
· Premature component failure.
· Decreased overall system performance.
Professional engineers and seasoned mechanics understand that investing in high-quality tools and parts is not an expense, but a strategic investment. The initial higher cost is rapidly offset by improved durability, reduced downtime, and enhanced performance.
Technological Innovations and Precision
Modern technological advancements have dramatically transformed our understanding and implementation of precision. Advanced manufacturing techniques like computer numerical control (CNC) machining, 3D printing, and laser cutting have enabled the creation of components with tolerances that were unimaginable just a few decades ago.
For performance enthusiasts, this means remarkable innovations like sophisticated blow off valves that can regulate pressure with incredible accuracy, ensuring optimal turbocharger performance and protecting critical engine components from potential damage.
The Art of Selection
Selecting the right tools and parts is an art form that requires deep technical knowledge, experience, and an understanding of system dynamics. It is not just about choosing the most expensive option, but understanding the specific requirements of a particular application.
Factors to consider include:
· Material composition.
· Manufacturing tolerances.
· Compatibility with existing systems.
· Performance characteristics.
· Environmental conditions.
· Maintenance requirements.
Case Studies in Precision
· Aerospace Engineering
In aerospace, precision is not just desirable—it is absolutely critical. A minor deviation in a turbine blade's design or a fractional imperfection in a critical component can lead to catastrophic failures with potentially fatal consequences.
· Medical Device Manufacturing
Medical devices represent another domain where precision is paramount. Surgical instruments, diagnostic equipment, and implantable devices must be manufactured with extreme accuracy to ensure patient safety and effective treatment.
· Automotive Performance Tuning
Performance enthusiasts understand that every modification must be carefully considered. Whether it is upgrading turbo accessories or fine-tuning an engine management system, precision determines the difference between incremental improvements and transformative performance gains.
· Training and Skill Development
Achieving and maintaining precision requires continuous learning and skill development. Professionals must stay updated with the latest technological advancements, manufacturing techniques, and industry best practices.
This involves:
· Ongoing technical education.
· Participation in workshops and seminars.
· Studying emerging technologies.
· Developing a deep understanding of materials science.
· Cultivating a mindset of continuous improvement.
Environmental and Economic Implications
Precision is not just about performance—it has significant environmental and economic implications. More precise manufacturing leads to:
· Reduced material waste.
· Lower energy consumption.
· Extended component lifespans.
· Improved resource efficiency.
By focusing on high-quality, precisely manufactured parts, industries can contribute to more sustainable and economically efficient production processes.
The Future of Precision
The concept of precision is poised for a transformative evolution as technological advancements redefine its possibilities across industries. As we move further into the digital age, emerging technologies promise to elevate the standards of accuracy, efficiency, and innovation in design and manufacturing.
Key Technologies Shaping the Future of Precision:
1. Artificial Intelligence (AI) and Machine Learning (ML)
AI and ML are revolutionising the way we approach precision by enabling predictive analytics, automated quality control, and enhanced decision-making. These technologies can identify patterns in complex datasets, optimise manufacturing processes, and anticipate defects before they occur, significantly improving efficiency and reducing waste.
2. Advanced Simulation Tools
Sophisticated simulation software allows engineers to model, test, and refine designs in virtual environments before physical production begins. These tools offer unprecedented accuracy, enabling real-time adjustments to parameters such as stress tolerances, thermal dynamics, and material properties, resulting in superior product performance.
3. Nanotechnology
Nanotechnology is unlocking precision at the molecular level. Applications range from creating ultra-strong, lightweight materials to designing nanoscale devices for medical and industrial use. By manipulating matter at an atomic scale, nanotechnology paves the way for innovations that were once unimaginable.
4. Quantum Computing
Quantum computing promises to solve complex calculations exponentially faster than traditional methods, transforming precision engineering. Its potential to analyse vast datasets and model intricate systems in real-time will allow for breakthroughs in material science, logistics, and high-stakes manufacturing processes.
5. Advanced Materials
The development of next-generation materials, such as graphene, shape-memory alloys, and bio-inspired composites, will enhance durability, adaptability, and precision. These materials open up new possibilities in industries ranging from aerospace to healthcare, enabling the creation of components with unparalleled specifications.
Implications for Engineering and Manufacturing:
· Enhanced Customisation: Technologies like 3D printing combined with AI will enable hyper-customised products tailored to individual requirements with micron-level accuracy.
· Sustainability Gains: Precision advancements will minimise waste, lower energy consumption, and optimise resource use, supporting greener manufacturing practices.
· Innovation Acceleration: Faster prototyping and testing cycles will shorten development timelines, allowing for quicker market entry of cutting-edge products.
The convergence of these technologies will not only redefine the limits of precision but also drive a paradigm shift in how industries innovate and operate. As the boundaries of what is possible expand, the future of precision promises to usher in an era of unprecedented technological and economic progress.
Precision is not a luxury—it is a necessity. Whether you are an engineer designing complex systems, a mechanic maintaining critical equipment, or a performance enthusiast pushing technological boundaries, the right tools and parts are your pathway to excellence.
Embrace precision. Invest in quality. Understand the intricate dance of components that transform good into extraordinary.
In a world of constant change and increasing complexity, precision remains the ultimate differentiator.