Step-by-Step Insight Into the Manufacturing of Flush Door in India
At Dhanvardhan Ply, only high-density seasoned hardwood is used for superior structural stability and strength.
Share this Post to earn Money ( Upto ₹100 per 1000 Views )
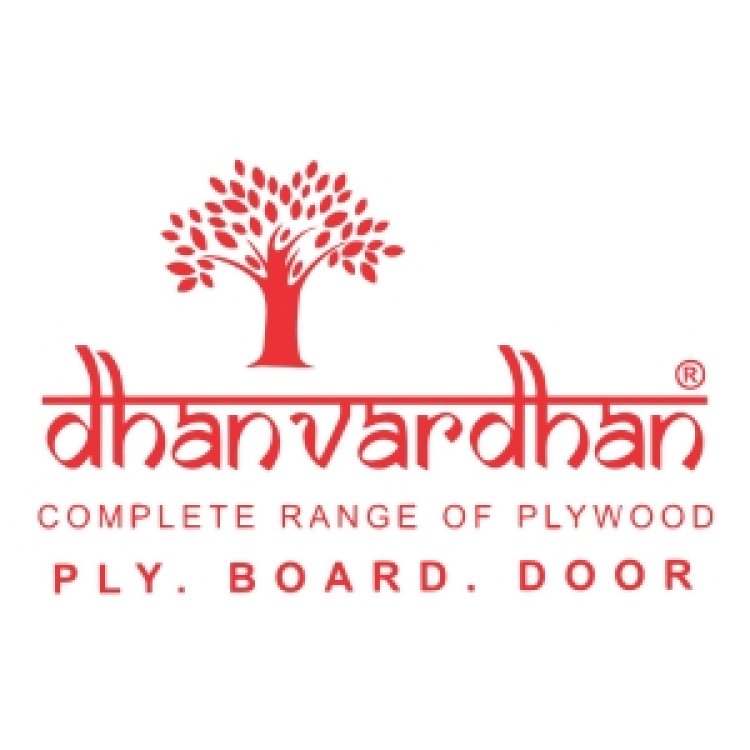
Flush doors are widely used in modern construction for both residential and commercial buildings due to their sleek look, durability, and affordability. As the demand continues to grow, so does the need for high-quality, precisely engineered flush doors. Understanding the Manufacturing of Flush Door in India gives insight into how brands like Dhanvardhan Ply ensure consistency, strength, and aesthetics in their products.
Here’s a comprehensive breakdown of how flush doors are manufactured in India, step-by-step.
Step 1: Selection of Core Material
The first step in the Manufacturing of Flush Door in India begins with the selection of core material, which forms the foundation of the door. The commonly used core materials include:
-
Solid wood battens (hardwood species like sal, teak, or mango)
-
Blockboard core or hollow core configurations
At Dhanvardhan Ply, only high-density seasoned hardwood is used for superior structural stability and strength.
Step 2: Cutting and Seasoning of Timber
Selected timber is cut into specific sizes and then seasoned to reduce moisture content. Proper seasoning is crucial for:
-
Preventing warping and twisting
-
Enhancing dimensional stability
-
Improving resistance to fungal decay
This step ensures the durability and longevity of the flush door, especially when it’s expected to resist weather changes.
Step 3: Core Assembly
After seasoning, the wooden battens are assembled edge-to-edge to form the door core. This core can be:
-
Solid Core – fully filled with battens
-
Hollow Core – partially filled to reduce weight and cost
The core is glued together using high-quality adhesives such as phenol-formaldehyde or urea-formaldehyde resins. These glues also contribute to the door’s water resistance when using BWP-grade materials.
Step 4: Fixing Face Veneers
Two face veneers (often made from high-quality plywood or MDF) are fixed on either side of the core using strong adhesives. These veneers serve multiple purposes:
-
Provide a smooth and aesthetic finish
-
Enhance the strength of the door
-
Create a surface suitable for painting, polishing, or laminating
This outer layer is what gives the door its final, refined appearance.
Step 5: Pressing
The assembled door structure is then pressed under high temperature and pressure in a hot press machine. This step helps:
-
Ensure uniform bonding
-
Eliminate air bubbles
-
Provide a flat, warp-free surface
At Dhanvardhan Ply, cutting-edge hydraulic presses are used to deliver consistency and smooth finishes in every door.
Step 6: Edge Banding & Finishing
After pressing, the edges of the flush door are trimmed and sealed using solid wooden lipping or edge bands. This prevents:
-
Moisture ingress from the sides
-
Splitting or cracking during installation
-
Termite infestation
The edges are also sanded for a smooth finish and precision in sizing.
Step 7: Treatment for Termite and Borer Resistance
To increase the door’s life, it is treated with anti-termite and anti-borer solutions. This step is particularly important in Indian climates where pests are a major concern.
As one of the Best Quality Waterproof Plywood Suppliers in India, Dhanvardhan Ply integrates pest-resistant treatments in their entire door and plywood range.
Step 8: Waterproofing (Optional for BWP Grade)
For BWP (Boiling Water Proof) flush doors, an additional waterproofing treatment is done. This involves:
-
Using phenol-bonded adhesives
-
Chemical impregnation
-
Water resistance testing
Flush doors meant for use in bathrooms, kitchens, or humid environments go through this enhanced treatment process.
Step 9: Trimming and Final Sizing
Post-treatment, each flush door is trimmed to the exact dimensions using high-precision cutting tools. This ensures:
-
Perfect fitting during installation
-
Consistency in standard sizes
-
No uneven or rough edges
Customized sizing is also offered by major manufacturers like Dhanvardhan Ply, depending on project requirements.
Step 10: Sanding and Surface Finishing
Next comes the sanding process to create a smooth and even surface, which is critical for:
-
Better application of paint or laminate
-
Professional-grade finish
-
Elimination of any surface imperfections
Flush doors are available in raw form, laminated, or pre-finished depending on the customer’s preference.
Step 11: Quality Inspection
Every door undergoes a stringent quality inspection to ensure it meets industry standards like IS 2202 (Part I) for wooden flush doors. The parameters checked include:
-
Thickness and size accuracy
-
Surface smoothness
-
Adhesion and bonding
-
Resistance to impact and moisture
-
Termite resistance
Dhanvardhan’s team ensures that only 100% tested doors reach the market – a practice that makes them one of the Best Flush Door Manufacturers in India.
Step 12: Packaging and Dispatch
Finally, the flush doors are packed with protective sheets or shrink wraps and dispatched to dealers, warehouses, or directly to construction sites. Careful packaging protects the doors during transit and ensures they reach customers in perfect condition.
Conclusion
The Manufacturing of Flush Door in India involves a meticulous process that balances craftsmanship with modern technology. From timber selection and core assembly to waterproofing and final inspection, each step determines the quality and lifespan of the finished product.
Brands like Dhanvardhan Ply have raised the bar in this industry by integrating advanced machinery, stringent quality control, and sustainable practices. Their dual reputation as one of the Best Flush Door Manufacturers and Best Plywood Manufacturers and Suppliers in India makes them a preferred choice for builders, architects, and homeowners across the country.