Maintenance 101: Keeping Your Tray Sealing Machine in Top Working Condition
Maintenance 101: Keeping Your Tray Sealing Machine in Top Working Condition
Share this Post to earn Money ( Upto ₹100 per 1000 Views )
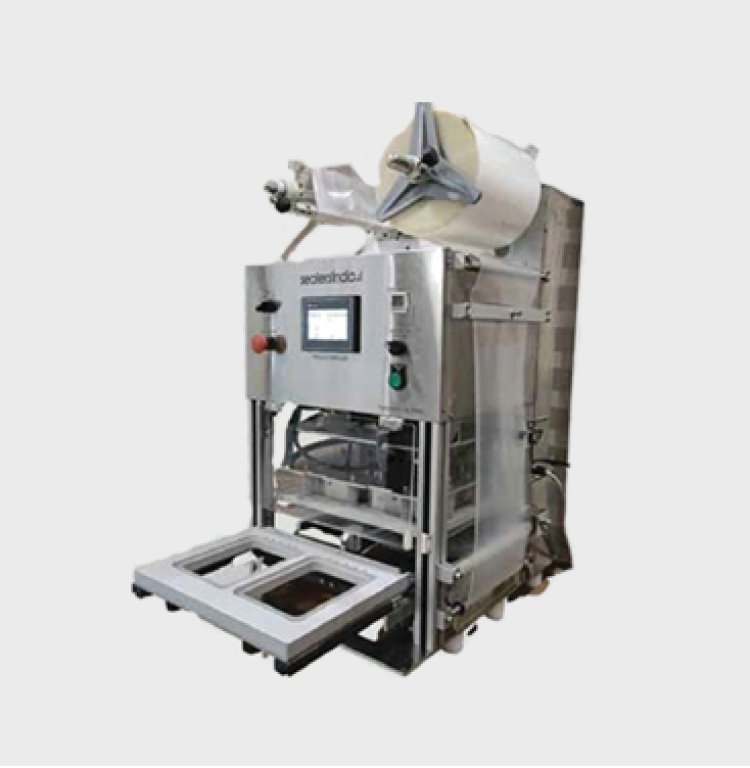
Tray sealing machines are a cornerstone of packaging operations in industries such as food processing, pharmaceuticals, and manufacturing. These machines efficiently seal products into trays, maintaining product freshness and quality. Like any industrial equipment, regular maintenance is essential to keep your tray sealing machine functioning at its best. Neglecting maintenance can lead to breakdowns, costly repairs, and downtime. This guide offers essential tips to keep your tray sealing machine in top condition.
1. Regular Cleaning of the Machine
Keeping your tray sealing machine clean is the most fundamental maintenance task. Residue from food products, oils, and adhesives can build up over time, affecting performance and even contaminating the sealed products. Daily cleaning, especially after a shift, ensures the machine remains hygienic and operates smoothly.
Use appropriate cleaning agents and soft cloths to wipe down all external surfaces and parts of the machine. Pay close attention to the sealing area, where residue is most likely to accumulate. Avoid using harsh chemicals that may corrode or damage the machine components. Regular cleaning not only maintains the hygiene standards but also prolongs the machine's life by preventing buildup that can lead to malfunctions.
2. Lubricate Moving Parts
Tray sealing machines have multiple moving components such as gears, bearings, and rollers. These parts experience constant friction, which can lead to wear and tear. Regular lubrication helps reduce friction, ensuring smooth operation and extending the life of the components.
Use manufacturer-recommended lubricants to avoid damaging the machine. Schedule lubrication at least once a week or as specified in the machine’s maintenance manual. Be careful not to over-lubricate, as excess oil or grease can attract dust and debris, which may clog the machinery. Proper lubrication minimizes breakdowns, reduces noise, and keeps your tray sealing machine running efficiently.
3. Check and Replace Worn Sealing Elements
The sealing elements, such as the sealing head and the heat plates, are critical to the tray sealing process. Over time, these elements can wear out, leading to weak seals or incomplete sealing. Regular inspection of these components helps ensure your tray sealing machine produces consistent, high-quality seals.
Look for signs of wear such as discoloration, warping, or thinning of the sealing elements. If you notice any issues, replace the parts promptly to avoid compromising the integrity of the sealed products. Using high-quality, compatible replacement parts will ensure that your machine continues to perform optimally.
4. Inspect Electrical Components
Tray sealing machines rely heavily on electrical systems to control their functions. Issues with wiring, connections, or control panels can lead to erratic performance or complete failure. Regular inspections of the electrical components help identify problems before they escalate.
Check for loose wires, frayed cables, or signs of burning around connections. Ensure that the control panels are functioning correctly and that the display shows accurate readings. If you find any electrical issues, consult a qualified technician for repairs. Regular electrical maintenance minimizes the risk of unexpected machine downtime and safety hazards.
5. Monitor Heat Settings and Calibration
The efficiency of a tray sealing machine depends heavily on accurate heat settings. Incorrect temperatures can lead to poorly sealed trays, affecting product quality. Regularly monitor and calibrate the heat settings to ensure they are within the required range for the materials being used.
Use a reliable thermometer to verify the temperature accuracy. Calibration should be done according to the manufacturer’s guidelines or whenever you notice irregularities in the sealing quality. Maintaining correct heat settings ensures consistent performance, reduces waste, and guarantees the longevity of the machine’s heating elements.
6. Check for Air Leaks in Pneumatic Systems
Many tray sealing machines use pneumatic systems for their operations, such as applying pressure during the sealing process. Air leaks in the pneumatic system can reduce efficiency and lead to improper sealing. Periodic checks for air leaks are crucial for maintaining optimal machine performance.
Inspect hoses, valves, and connectors for signs of leaks. Listen for hissing sounds or use a soapy water solution to detect leaks visually. Promptly repair or replace damaged components to maintain pressure consistency. A well-maintained pneumatic system ensures efficient operation and reliable sealing.
7. Check and Tighten Fasteners
With continuous operation, vibrations from the tray sealing machine can cause screws, bolts, and other fasteners to loosen over time. Loose fasteners can lead to misalignments, excessive noise, or even damage to machine parts. Regularly checking and tightening fasteners helps maintain the machine’s structural integrity.
Create a routine checklist to inspect all critical fasteners. Ensure that screws and bolts are tightened to the manufacturer’s specifications. Avoid overtightening, as this may strip the threads or damage the components. Keeping the fasteners secure ensures smooth and safe operation of the machine.
8. Replace Filters and Gaskets Periodically
Filters and gaskets play an essential role in maintaining the efficiency and cleanliness of your tray sealing machine. Filters in pneumatic systems or cooling units can become clogged with debris, reducing performance. Gaskets, on the other hand, help maintain seals and prevent leaks.
Replace filters and gaskets as part of your routine maintenance schedule. Consult the manufacturer’s recommendations for the appropriate replacement intervals. Clean filters regularly to extend their lifespan, but ensure timely replacement to prevent machine inefficiencies or contamination issues.
9. Train Operators on Proper Usage
One of the best ways to maintain your tray sealing machine is by ensuring operators are well-trained in its use. Misuse or incorrect operation can lead to unnecessary wear, damage, or breakdowns. Regular training sessions help operators understand the correct procedures and the importance of maintenance.
Provide clear guidelines on machine operation, cleaning, and basic troubleshooting. Encourage operators to report any irregularities immediately to prevent small issues from escalating. Well-trained staff ensure that the machine operates at peak efficiency and reduces the risk of damage caused by user error.
10. Schedule Professional Maintenance Inspections
Even with routine in-house maintenance, scheduling professional inspections is essential to keep your tray sealing machine in top condition. Technicians have specialized knowledge and tools to identify and address issues that may not be visible during regular checks.
Plan for professional inspections at least once or twice a year, depending on the machine’s usage. These inspections can identify potential problems early, ensuring that the machine continues to function optimally. Investing in professional maintenance helps extend the machine’s lifespan and avoid costly repairs in the future.
Conclusion
Regular maintenance is the key to keeping your tray sealing machine or in top working condition. The same applies if you are using a cup sealing machine. From cleaning and lubrication to professional inspections and operator training, each step contributes to the machine’s efficiency and longevity. By implementing these maintenance practices, you can avoid costly downtime, ensure product quality, and get the most value out of your investment.