ISO 13485 Internal Auditor Training: From Basics to Pro
Elevate your skills with ISO 13485 Internal Auditor Training. Gain expertise in auditing, compliance, and quality management for medical devices
Share this Post to earn Money ( Upto ₹100 per 1000 Views )
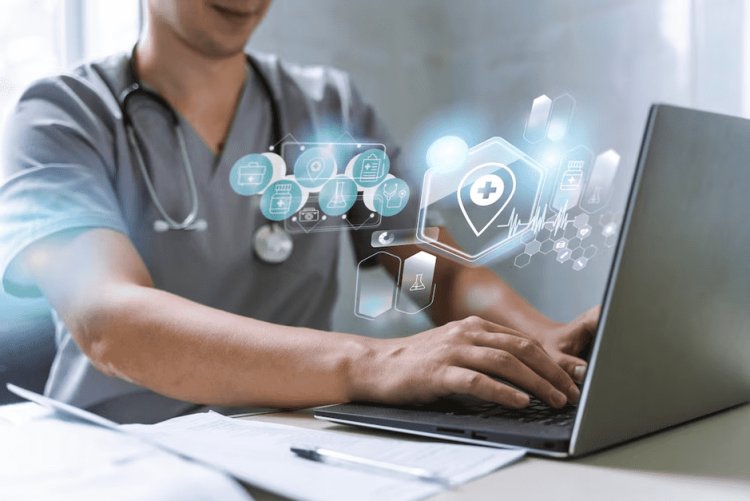
Internal auditing isn’t just about checking boxes or following procedures—at least, not if you’re doing it right. It’s about ensuring that a medical device company’s quality management system (QMS) functions as it should. It’s about catching inconsistencies before they turn into compliance nightmares. And it’s about making sure that every process, from design to distribution, meets the rigorous standards of ISO 13485.
If you’re here, chances are you’re looking to build (or sharpen) your internal auditing skills under ISO 13485, the gold standard for medical device quality. Whether you're stepping into an internal auditor role for the first time or refining your expertise, this guide will walk you through what it takes to become an effective internal auditor for medical device companies.
We’ll cover what the training entails, what skills you need, how audits should be conducted, and why your role is more than just compliance—it’s about ensuring quality that directly impacts patient safety.
Why Internal Auditing in Medical Devices Matters More Than You Think
Auditing isn’t the most glamorous job. It doesn’t have the thrill of designing a new pacemaker or the prestige of launching a groundbreaking surgical instrument. But without internal auditors, the entire system can crack.
Medical devices directly impact human lives. That means any misstep in manufacturing, testing, or compliance could have serious consequences. A faulty knee implant? A pacemaker that doesn’t work as expected? The risk is too great.
That’s where internal auditors come in. They’re the gatekeepers, the ones who check that every part of the quality system works exactly as it should—before an external auditor, regulatory authority, or (worst-case scenario) a product failure exposes the gaps.
So, how do you get there? Let’s start with the foundation: training.
ISO 13485 Internal Auditor Training: What to Expect
Training programs for ISO 13485 internal auditors vary, but most will cover:
-
The core principles of ISO 13485 and how it applies to medical device companies
-
Internal auditing fundamentals (objectives, planning, execution, and reporting)
-
Risk-based thinking and process-based auditing
-
Common nonconformities and how to address them
-
How to prepare for external audits
Some training programs are instructor-led, while others are self-paced online courses. Many combine theoretical learning with practical exercises—because let’s be honest, reading about auditing and actually conducting an audit are two very different things.
A good training program should teach you not just how to audit, but how to think like an auditor.
That means knowing:
-
What to look for (the difference between a minor inconsistency and a major red flag)
-
How to ask the right questions (without leading or intimidating auditees)
-
How to document findings clearly (so that corrective actions are easy to implement)
But before we get ahead of ourselves, let’s talk about what ISO 13485 is actually built on.
ISO 13485: The Pillars of Medical Device Quality Management
ISO 13485 is all about consistency, risk management, and compliance. While it shares similarities with ISO 9001 (the general quality management standard), ISO 13485 is laser-focused on the medical device industry.
Here’s what it emphasizes:
-
Documented Procedures: Every process should be clearly documented, from design to production to post-market surveillance.
-
Risk-Based Thinking: Identifying risks early on prevents bigger problems down the road.
-
Regulatory Compliance: ISO 13485 aligns with global regulatory requirements (think FDA, EU MDR, Health Canada, etc.).
-
Product Safety & Efficacy: At the end of the day, the goal is to ensure safe, effective medical devices.
Internal auditors need to know these principles inside and out. That’s because auditing isn’t just about checking whether procedures exist—it’s about assessing whether they actually work.
What Makes a Great Internal Auditor?
Not everyone is cut out for auditing. It takes a specific mindset and skill set.
Key Traits of an Effective ISO 13485 Internal Auditor:
-
Attention to Detail – The small things matter. An overlooked process deviation could mean a major compliance issue later.
-
Critical Thinking – You can’t take everything at face value. Sometimes, the deeper issue isn’t immediately obvious.
-
Objectivity – An auditor’s job isn’t to make friends—it’s to ensure compliance. That means being fair but firm.
-
Communication Skills – You need to ask the right questions, explain findings clearly, and sometimes deliver tough news.
-
Knowledge of ISO 13485 & Regulations – Without this, you won’t know what’s acceptable and what’s not.
Got these skills? Great. Now let’s get into the auditing process itself.
The Internal Auditing Process (Step by Step)
1. Planning the Audit
Before you even step into an audit, you need a plan. That includes:
-
Defining audit objectives and scope
-
Reviewing previous audits and corrective actions
-
Preparing an audit checklist
2. Conducting the Audit
This is where you evaluate processes, interview employees, and review documentation. Keep these things in mind:
-
Ask open-ended questions (“Can you walk me through this process?” instead of “Is this process followed?”)
-
Look for objective evidence—don’t rely on verbal confirmation
-
Observe how procedures are actually followed (not just how they’re written)
3. Documenting & Reporting Findings
Once the audit is complete, findings need to be documented. A solid audit report includes:
-
Nonconformities (major or minor)
-
Observations (potential risks that don’t yet violate requirements)
-
Recommendations for corrective actions
4. Follow-Up & Corrective Actions
An audit doesn’t end when the report is written. Corrective actions must be implemented and verified in follow-up audits.
Common Audit Findings & How to Handle Them
Even the best-run companies have nonconformities. Some of the most common ones include:
-
Inadequate Document Control – Missing, outdated, or incorrect procedures
-
Training Deficiencies – Employees not properly trained on QMS procedures
-
Supplier Control Issues – Lack of oversight for outsourced processes
-
Incomplete Risk Management Documentation – Failure to assess and mitigate risks properly
How do you address findings?
-
Minor issues can often be fixed with process adjustments or retraining.
-
Major issues may require in-depth root cause analysis and corrective action plans.
-
Systemic issues might signal deeper problems that need top-level management attention.
Final Thoughts: More Than Just Compliance
ISO 13485 internal auditing isn’t just about avoiding trouble with regulators—it’s about ensuring medical devices are safe, effective, and reliable.
A strong internal audit program doesn’t just identify issues—it drives continuous improvement. And a great internal auditor isn’t just a compliance checker—they’re a quality champion.
So, if you’re stepping into this role, know that your work has real-world impact. And if you’re already an experienced auditor? Keep sharpening your skills. The industry is always evolving, and staying ahead of the curve means staying informed, adaptable, and, most importantly, committed to quality.