Inconel Bars in Submarine Accessories: Ensuring Durability in Extreme Conditions
Share this Post to earn Money ( Upto ₹100 per 1000 Views )
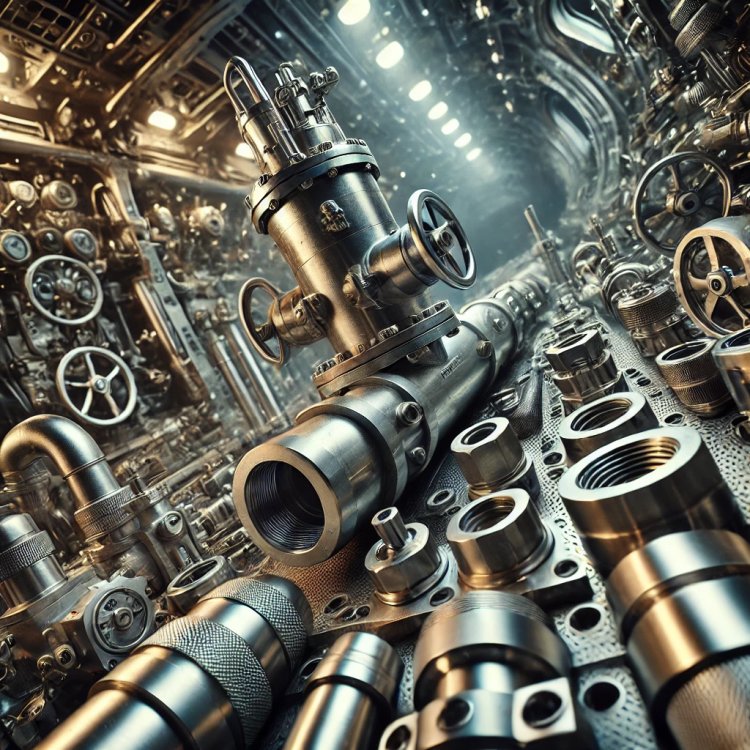
Submarines operate in perhaps the most hostile environment on earth, which includes high pressure, extreme temperature, and incessant exposure to aggressive seawater. To withstand this hostile condition, submarine parts need to be quite strong and, at the same time, highly reliable. Among the current options employed in submarine accessories are Inconel Bars, specifically Inconel 925 Bars.
Why Make A Choice Of Inconel Bars For Submarine Accessories
Inconel 925 bars are a superalloy with excellent resistance to corrosion, oxidation, and high temperatures, which makes them suitable for demanding applications such as submarine construction. Here's why Inconel bars are used in submarine accessories:
Corrosion Resistance The submarines are submerged in the sea, which has naturally salty and mineralized water that can lead to corrosion in many metals. Inconel 925 Bars are known for superior resistance to seawater or any other aggressive chemical environments. The alloy forms a protective oxide layer of defence on the surface, thus ensuring that the submarine components do not rust and corrode, ensuring the prolonged use of submarine components.
The submarine systems, especially the ones on parts of propulsion and power generation, run very hot. The Inconel 925 Bars have high strength at elevated temperatures and even sustain structural integrity to support applications at very hot temperatures. This property has made them available for critical submarine components, such as exhaust systems, heat exchangers, propulsion mechanisms, and other supercritical applications in general.
Resistance to Stress Corrosion Cracking Besides general corrosion, submarines are also susceptible to another kind of corrosion known as stress corrosion cracking, especially in deep seas, where the pressure and chemical exposures are higher. Inconel 925 Bars resist stress corrosion cracking adequately and have used components with extreme pressure and environmental stresses, such as pressure vessels and submarine hulls.
Strength and Toughness Since Inconel 925 Bars possess both high and low-temperature strength, the structural parts in submarine accessories components require them. These bars are considered to be of sufficient strength for submarine accessories to meet the stress imposed by extreme underwater pressure, and even submarines would remain intact and operational under this kind of tremendous stress.
Main Applications of Inconel Bars in Submarine Accessories
Submarine Shells and Pressure Vessels The outer shell and pressure vessels of a submarine have to withstand vast water pressure at great depths. Inconel 925 Bars are used for the strength, durability, and corrosion resistance in the making of such structures. These bars are generally incorporated in the hulls, pressure-compensated compartments, and other critical areas.
Propulsion Systems The propulsion systems of the submarine contain components, including a turbine and heat exchanger. The components operate at high temperatures and also experience aggressive gases and fluids, for which Inconel 925 Bars are utilized in these systems to provide efficient operation and durability during long periods of time. Oxidation resistance, along with thermal cycling capability from Inconel alloys, ensures submarine propulsion component longevity.
Electrical and Electronic Components Submarines require electrical systems that can be operated under severe conditions. Inconel 925 Bars are preferably used in electrical components where lots of currents are run, temperatures fluctuate, and a corrosive marine environment is encountered in their duty. They can be used for electrical connectors, switches, and other critical components because of their durability and conductivity.
Welding and Fabrication of Submarine Parts Submarine parts are welded using Inconel 925 Bars, which are known not to lose corrosion resistance during the welding process while maintaining strength, therefore presenting a good choice in submarine construction. The bars can be utilized to weld submarine parts in order to provide strong and durable joints that can withstand the structural integrity of the vessel.
Conclusion
The Inconel bars, particularly the Inconel 925 Bars, cannot be compared to any other in terms of their strength and resistance to extreme conditions. They become crucial in the construction and maintenance of submarine accessories. Their resilience and resistance to pressure, their performance under high temperatures, and their resistance to corrosion ensure that submarine components continue functioning reliably in the most underwater hostile environments. The demand will continue to be further boosted by high-performance materials such as Inconel 925 Bars, whose critical importance to submarine safety, performance, and longevity will continue to be at its peak.
To get the best quality Inconel 925 Bars for your submarines or for other marine projects, please contact us to learn how these superalloys can help your projects reach their extreme end.