How Plastic Polymers Are Revolutionizing 3D Printing Technologies
3D printing has changed the way we create things. It allows us to make objects layer by layer, directly from a digital design. This technology is used in many fields, such as medicine, manufacturing, education, and even art. At the heart of this innovation lies the material used to build these objects — and plastic polymers are leading this revolution.
Share this Post to earn Money ( Upto ₹100 per 1000 Views )
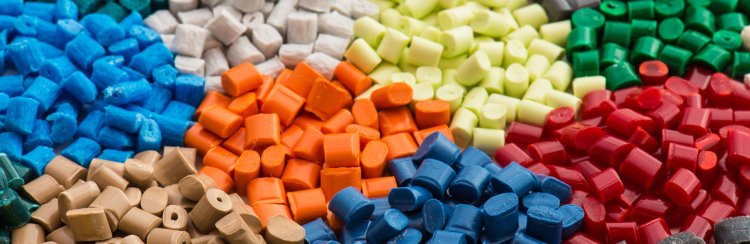
In this article, we will explore how plastic polymers are transforming 3D printing, why plastic polymers are so important, and how Duha Industries is playing a key role in this exciting field.
What is 3D Printing?
Before diving into plastic polymers, let's understand 3D printing in simple terms. Imagine you want to make a small model of a car. Traditionally, you would need to carve it from wood or mold it using complicated tools. With 3D printing, you simply create a digital design of the car on a computer and send it to a 3D printer. The printer then builds the car layer by layer using a special material.
This process is called additive manufacturing because the object is made by adding material step by step. 3D printing can create complex shapes that are difficult or impossible to make by traditional methods.
What are Plastic Polymers?
Plastic polymers are long chains of molecules made from small repeating units called monomers. These polymers have unique properties that make them useful for many applications. For example, some plastics are very strong, while others are flexible or heat-resistant.
In 3D printing, plastic polymers serve as the "building blocks" for creating objects. They come in different types, each with its own strengths and weaknesses. Common types include:
-
PLA (Polylactic Acid): Made from natural materials like corn starch, it is easy to print and biodegradable.
-
ABS (Acrylonitrile Butadiene Styrene): Strong and durable, often used for making toys and automotive parts.
-
PETG (Polyethylene Terephthalate Glycol): Clear, strong, and flexible, used for containers and mechanical parts.
-
Nylon: Very strong and flexible, great for industrial parts.
-
TPU (Thermoplastic Polyurethane): Flexible and elastic, used for items like phone cases and shoes.
Each polymer type can be melted and shaped by 3D printers to create detailed and precise objects.
Why Plastic Polymers Are Key to 3D Printing
Plastic polymers have many qualities that make them ideal for 3D printing:
1. Ease of Use
Plastic polymers can be melted and reshaped repeatedly, which suits the layering process of 3D printing. This means printers can build complex shapes with high accuracy.
2. Cost-Effective
Compared to metals or ceramics, plastics are generally cheaper. This lowers the cost of producing prototypes and custom products, making 3D printing accessible for many industries.
3. Versatility
Different plastic polymers offer a wide range of properties — from rigid and strong to soft and flexible. This variety means 3D printing can create parts for many uses, from delicate medical devices to tough automotive components.
4. Lightweight
Plastic parts are much lighter than metal or ceramic parts, which is crucial in industries like aerospace and automotive, where weight savings improve performance and reduce fuel consumption.
5. Sustainability
Newer plastics like PLA are made from renewable resources and are biodegradable, helping reduce environmental impact. This makes 3D printing with plastics more eco-friendly.
How Plastic Polymers Are Transforming Industries
Plastic polymers are not only changing 3D printing but also transforming many industries. Here’s a look at some of the major sectors benefiting from this technology:
Medical Industry
3D printing is revolutionizing healthcare. Plastic polymers enable the creation of customized implants, prosthetics, and surgical tools. For example, doctors can print a plastic model of a patient’s organ to plan surgery better. Prosthetic limbs made from plastic polymers can be lightweight and tailored exactly to the patient’s needs.
Automotive and Aerospace
Plastic polymers allow car and airplane manufacturers to quickly produce lightweight, durable parts. This reduces production time and costs, and the lightweight nature of plastics improves fuel efficiency. Complex parts with intricate designs can be 3D printed, which were impossible to make before.
Education and Research
Schools and universities use 3D printing with plastic polymers to teach students about design and engineering. It allows hands-on learning where students can bring their ideas to life. Researchers can also rapidly prototype new inventions.
Consumer Goods and Fashion
3D printing is now common in making custom jewelry, shoes, and even clothing accessories. Plastic polymers offer flexibility and strength, allowing designers to experiment with new styles and personalized products.
Construction and Architecture
Plastic polymers in 3D printing help build models of buildings and even actual components for construction. This technology helps architects and builders visualize designs and reduce waste by printing only what is needed.
Challenges with Plastic Polymers in 3D Printing
Even though plastic polymers are revolutionary, there are still challenges to overcome:
-
Strength Limitations: Some plastics may not be as strong as metals or composites for certain applications.
-
Heat Resistance: Many plastics can soften or deform at high temperatures.
-
Surface Finish: Sometimes 3D printed plastic parts require extra finishing for smoothness or appearance.
-
Environmental Concerns: Not all plastics are biodegradable, so waste management is important.
Despite these issues, ongoing research and innovations are continuously improving the quality and sustainability of 3D printing plastics.
Duha Industries: Leading the Way in Plastic Polymers for 3D Printing
At the forefront of this revolution is Duha Industries, a company dedicated to developing high-quality plastic polymers specially designed for 3D printing applications.
What Makes Duha Industries Different?
-
Innovative Polymer Development
Duha Industries invests heavily in research to create new polymer formulations that improve strength, flexibility, and printing ease. Their polymers are engineered to work seamlessly with the latest 3D printers, ensuring consistent quality.
-
Sustainability Focus
Duha Industries is committed to eco-friendly products. They offer biodegradable and recyclable polymers, helping companies reduce their carbon footprint while still benefiting from advanced 3D printing technology.
-
Wide Range of Products
Whether you need a flexible polymer for wearable devices or a tough plastic for industrial parts, Duha Industries has a solution. Their product range covers PLA, ABS, PETG, Nylon, TPU, and more — all optimized for 3D printing.
-
Customer Support and Training
Understanding 3D printing materials can be challenging. Duha Industries provides excellent customer service, including technical support and training programs, to help businesses and individuals get the most out of their 3D printing projects.
How Duha Industries Polymers Improve 3D Printing
By choosing Duha Industries’ polymers, users benefit in many ways:
-
Better Print Quality: The polymers have consistent melting points and flow properties, reducing printing errors.
-
Faster Printing: Optimized materials allow quicker layering without losing detail or strength.
-
Durability: Finished parts are more resistant to wear, impact, and environmental factors.
-
Customization: Duha’s polymers can be tailored to specific needs, such as color, flexibility, or strength.
Real-World Examples of Duha Industries’ Impact
Manufacturing Prototypes
Many companies use Duha Industries’ polymers to create prototypes quickly. This speeds up product development and allows designers to test and improve their ideas before mass production.
Medical Devices
Hospitals and medical device manufacturers use Duha polymers to print custom implants and surgical tools. The materials are biocompatible and safe for patients.
Education
Schools that partner with Duha Industries can provide students with reliable 3D printing materials that encourage creativity and innovation.
The Future of 3D Printing with Plastic Polymers
Plastic polymers will continue to shape the future of 3D printing in exciting ways:
-
Smart Polymers: Materials that change properties based on temperature or light could create adaptable and responsive parts.
-
Recycled Polymers: More 3D printing materials will come from recycled plastics, reducing waste.
-
Multi-Material Printing: Combining different polymers in one print can produce parts with varied properties in a single object.
-
Biomedical Advances: Biodegradable polymers will lead to 3D printed tissues and organs for medical use.
Duha Industries is actively working on these developments, ensuring they stay at the cutting edge of polymer technology for 3D printing.
Conclusion
Plastic polymers are truly revolutionizing 3D printing. They offer flexibility, cost-effectiveness, and a wide range of properties that make 3D printing accessible and useful for many industries. Companies like Duha Industries are leading the charge by developing advanced polymer materials that improve print quality, durability, and sustainability.
As 3D printing technology grows, the role of plastic polymers will become even more important. Whether you are a manufacturer, healthcare provider, educator, or hobbyist, plastic polymers from Duha Industries can help you unlock the full potential of 3D printing.
The future of creating objects, products, and solutions is here — and plastic polymers are at its heart.
If you want to learn more about Duha Industries and their innovative plastic polymers for 3D printing, visit their website or contact their experts today.