How do top granite manufacturers maintain consistency in color and quality across large orders?
Granite, a natural stone known for its durability and aesthetic appeal, is widely used in various applications such as countertops, flooring, and exterior facades.
Share this Post to earn Money ( Upto ₹100 per 1000 Views )
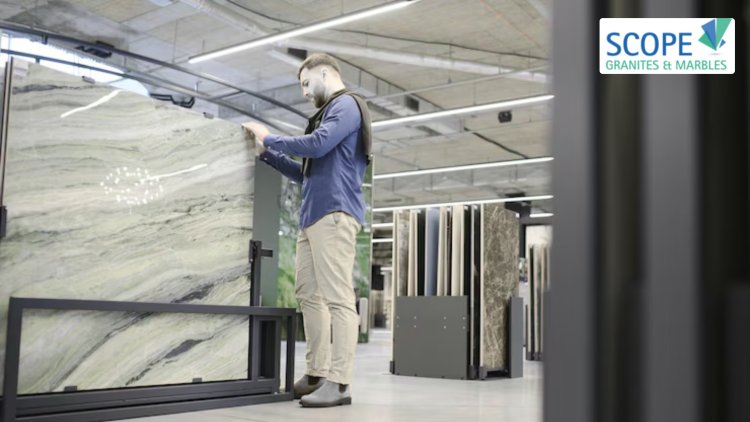
Introduction:
Granite, a natural stone known for its durability and aesthetic appeal, is widely used in various applications such as countertops, flooring, and exterior facades. However, maintaining consistent color and quality across large orders can be challenging due to its inherent variations in mineral composition and texture. Top granite manufacturers utilize several strategies to ensure that their products meet customer expectations consistently.
Sourcing from Trusted Quarries:
To maintain consistency, reputable granite manufacturers carefully select and source granite from well-established quarries. These quarries are known for producing high-quality, consistent slabs. By working closely with a limited number of trusted quarries, manufacturers can better control the quality and color variations of the granite they procure. This helps them minimize the risk of receiving batches with noticeable differences.
Advanced Sorting and Inspection Processes:
Once the granite slabs are extracted, manufacturers employ advanced sorting techniques to assess the color, veining, and overall quality of each slab. With the help of modern technology, they can categorize slabs based on their color and texture. Automated systems, along with manual inspections by experienced professionals, help detect any imperfections or inconsistencies. This rigorous sorting process ensures that only slabs of uniform quality are selected for production.
Consistent Mixing and Blending of Slabs:
Granite slabs from the same quarry may still have slight differences in color or pattern. To address this, top manufacturers use a blending technique during production. They mix slabs from different sections of the quarry or batches to achieve a uniform appearance. This process ensures that the final product, whether for a small kitchen countertop or a large commercial project, exhibits consistent color and pattern, minimizing noticeable variations.
Quality Control and Testing:
Regular quality control checks are crucial in maintaining the consistency of granite products. Leading manufacturers implement a series of tests to assess the durability, strength, and appearance of the granite slabs. These tests may include hardness tests, stain resistance tests, and surface polishing evaluations. By conducting these tests at various stages of production, manufacturers can ensure that the finished product meets industry standards and customer specifications.
Customization and Precision Cutting:
For large orders, manufacturers often offer customized solutions to meet specific requirements. This may involve precision cutting and polishing techniques to ensure that the final products fit seamlessly together. Advanced cutting machinery and CNC (Computer Numerical Control) technology allow for highly accurate measurements and cuts, ensuring that pieces of granite fit perfectly and maintain consistent color alignment across a larger installation. This attention to detail results in an aesthetically pleasing and uniform appearance.
Comprehensive Supply Chain Management:
Top granite manufacturers also maintain a tight control over their supply chains. From procurement to shipping, each step is carefully monitored to ensure that the quality and color of the granite remain consistent throughout the entire process. Supply chain transparency helps identify potential issues early, whether in the extraction, transportation, or distribution stages. By staying ahead of potential challenges, manufacturers can guarantee that large orders are fulfilled with consistent results, even when they are sourced from different batches or regions.
Communication with Clients:
Transparency and communication play a vital role in ensuring client satisfaction. Manufacturers frequently communicate with clients to understand their specific needs regarding color consistency and quality. They provide samples and renderings to showcase what the final product will look like, allowing clients to approve the granite before production begins. This collaboration helps to align expectations and ensures that the final product matches the desired specifications.
Post-Production Adjustments and Treatments:
Even after the granite is processed, manufacturers apply various treatments to enhance the uniformity of the stone. This includes the application of sealants, polishing, and coloring agents that can help reduce any visible inconsistencies. These treatments improve both the aesthetic appeal and the durability of the stone, ensuring that the finished product is consistent in both appearance and quality. Additionally, post-production checks are performed to verify that the granite meets the client’s specifications and industry standards.
Conclusion:
By implementing these strategies, top granite manufacturers can deliver large orders with consistent color and quality, meeting the high standards expected by both residential and commercial clients. This level of precision and attention to detail ensures customer satisfaction and helps build trust in the brand’s reputation. Whether the project involves a single countertop or an expansive commercial installation, maintaining consistency in granite color and quality is critical to achieving a polished and professional result.