Comprehensive Guide to Automatic Visual Inspection Machine Qualification India and Particle Contamination Testing India
Automatic Visual Inspection Machine Qualification India is essential for validating the performance of automated inspection systems used in detecting defects in vials, ampoules, and other pharmaceutical packaging.
Share this Post to earn Money ( Upto ₹100 per 1000 Views )
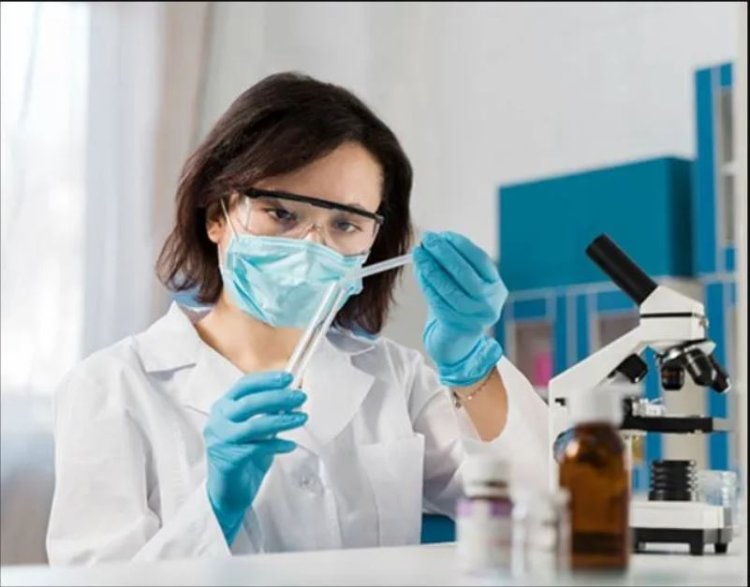
Quality assurance is a critical aspect of pharmaceutical and manufacturing industries, where precise inspection methods ensure product integrity and compliance. Automatic Visual Inspection Machine Qualification India is essential for validating the performance of automated inspection systems used in detecting defects in vials, ampoules, and other pharmaceutical packaging. Additionally, Particle Contamination Testing India helps in identifying unwanted particles in drugs and medical devices, ensuring safety and regulatory adherence. This article explores the visual inspection process, the Knapp test, the Knapp Kushner method, and the role of visual inspection in non-destructive testing (NDT).
What is Required for Visual Inspection?
Visual inspection in the pharmaceutical industry involves both manual and automated processes to detect particulate contamination, cracks, or seal integrity issues. The key requirements for an effective Automatic Visual Inspection Machine Qualification India include:
- Calibration and Validation: The machine must be calibrated and qualified to meet regulatory standards, ensuring reliable defect detection.
- High-Resolution Cameras: Advanced imaging technology helps identify even the smallest defects.
- Lighting and Contrast Optimization: Proper illumination improves detection accuracy.
- Standardized Defect Samples: Predefined defective samples, including those used in Particle Contamination Testing India, help in machine validation.
- Regulatory Compliance: The system must adhere to guidelines from the US FDA, EMA, and Indian Pharmacopeia.
What is the Knapp Test?
The Knapp Test is a pharmaceutical quality control method used to evaluate the effectiveness of container closure integrity. It assesses whether a container closure system can prevent microbial contamination and gas exchange. In Particle Contamination Testing India, the Knapp Test helps verify whether particulate contamination can penetrate packaging materials.
What is the Knapp Kushner Method?
The Knapp Kushner Method is a specific technique used in pharmaceutical inspection to evaluate the performance of automated visual inspection systems. It involves using controlled challenge samples with known defects to determine:
- The machine’s defect detection rate.
- The probability of false positives and false negatives.
- The system’s reliability in detecting particulate contamination.
This method plays a crucial role in Automatic Visual Inspection Machine Qualification India, ensuring the inspection system meets industry standards for defect detection accuracy.
What is Visual Inspection in NDT?
Visual inspection in Non-Destructive Testing (NDT) refers to the process of examining materials, components, or finished products for defects without causing any damage. It is widely used in industries such as aerospace, automotive, and pharmaceuticals. Automatic Visual Inspection Machine Qualification India applies NDT principles to pharmaceutical packaging, ensuring that defects are detected early without compromising product integrity.
Conclusion
Both Automatic Visual Inspection Machine Qualification India and Particle Contamination Testing India are vital for maintaining high-quality standards in pharmaceuticals and manufacturing. Automated visual inspection systems ensure accurate defect detection, while particle contamination testing prevents unwanted impurities in medical products. By implementing advanced inspection techniques and rigorous validation processes, companies can enhance product safety, regulatory compliance, and overall quality assurance.