A Deep Dive into Non Conformance CAPA Reporting and Analysis
In today’s highly regulated and competitive industries, effective quality management is paramount. One critical component of maintaining high standards is the Non Conformance CAPA (Corrective and Preventive Action) process. This comprehensive blog explores the intricacies of Non Conformance CAPA reporting and analysis, providing valuable insights for professionals in the Life Sciences and Manufacturing sectors. We will delve into advanced strategies, integration with modern platforms, and future trends that can help organizations stay ahead in their quality management endeavors.
Share this Post to earn Money ( Upto ₹100 per 1000 Views )
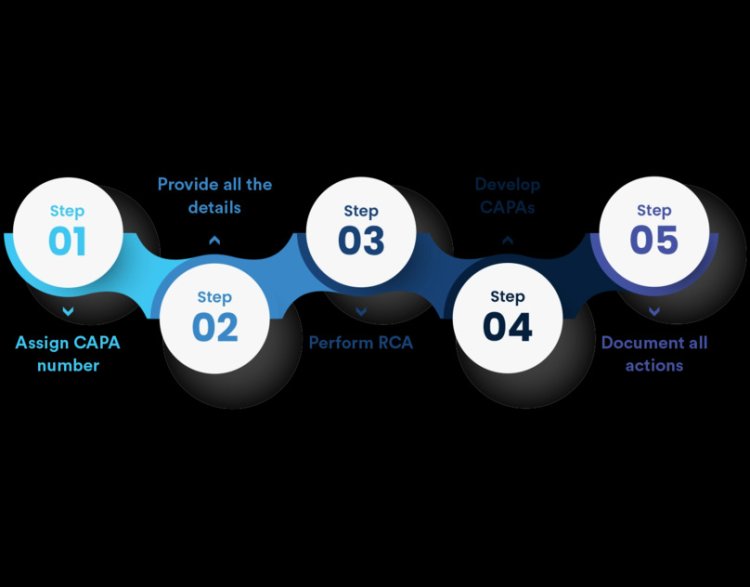
The Strategic Importance of Non Conformance CAPA in Quality Management Systems
Enhancing Compliance and Reducing Risks
Non Conformance CAPA plays a pivotal role in ensuring that organizations adhere to regulatory standards. By systematically addressing deviations and implementing corrective actions, companies can mitigate risks associated with product defects and non-compliance. This is particularly crucial in industries such as pharmaceuticals, medical devices, and complex manufacturing, where regulatory scrutiny is intense and the cost of non-compliance can be substantial.
Building a Culture of Continuous Improvement
Implementing an effective Non Conformance CAPA process fosters a culture of continuous improvement. It encourages organizations to proactively identify and rectify issues, leading to enhanced product quality and operational efficiency. This ongoing commitment to quality not only satisfies regulatory requirements but also boosts customer satisfaction and trust.
Integrating Non Conformance CAPA with Advanced PLM and QMS Platforms
Seamless Data Integration for Enhanced Decision-Making
Integrating Non Conformance CAPA with Product Lifecycle Management (PLM) and Quality Management Systems (QMS) platforms ensures seamless data flow across various departments. This integration facilitates real-time monitoring and analysis of non-conformances, enabling informed decision-making. For instance, CAPA in manufacturing, this integration can help identify recurring issues in production lines, allowing for timely interventions and process optimizations.
Facilitating Cross-Functional Collaboration
Advanced platforms promote collaboration between different teams, such as quality assurance, regulatory affairs, and production. This collaborative approach ensures that all stakeholders are aligned in addressing non-conformances, leading to more effective and sustainable corrective actions. In the pharmaceutical industry, where multifaceted processes are involved, such integration is indispensable for maintaining high standards of quality and compliance.
Leveraging Data Analytics for Non Conformance CAPA Analysis
Predictive Analytics for Proactive Quality Management
Data analytics transforms Non Conformance CAPA from a reactive to a proactive process. By analyzing historical data, organizations can identify patterns and predict potential non-conformances before they occur. This predictive capability is invaluable in capa medical device industries, where anticipating issues can prevent costly recalls and ensure patient safety.
Identifying Root Causes with Advanced Analytical Tools
Advanced analytical tools enable deeper insights into the root causes of non-conformances. Techniques such as root cause analysis (RCA) and failure mode and effects analysis (FMEA) can be integrated into the CAPA process to systematically identify and address underlying issues. This thorough approach ensures that corrective actions are not just superficial fixes but address the fundamental problems.
The Impact of Non Conformance CAPA on Supply Chain Management
Ensuring Supplier Quality and Compliance
Non Conformance CAPA extends beyond internal processes to include supplier management. By implementing CAPA processes within the supply chain, organizations can ensure that suppliers adhere to quality standards. This is particularly important in the manufacturing sector, where supplier-related non-conformances can disrupt production and compromise product quality.
Enhancing Supplier Collaboration and Performance
Effective CAPA processes foster better collaboration with suppliers, leading to improved performance and reliability. Regular feedback and corrective actions help suppliers understand and meet the quality expectations, resulting in a more robust and resilient supply chain. This collaborative approach is essential for maintaining consistent quality across all stages of production.
Enhancing Product Lifecycle with Non Conformance CAPA Reporting
Continuous Improvement Across Product Stages
Non Conformance CAPA is integral to managing the entire product lifecycle, from design and development to manufacturing and post-market surveillance. By continuously monitoring and addressing non-conformances at each stage, organizations can enhance product quality and reduce time-to-market.CAPA in manufacturing, this continuous improvement ensures that products meet evolving market demands and regulatory requirements.
Facilitating Regulatory Compliance and Certification
Comprehensive CAPA reporting supports regulatory compliance and certification processes. Detailed documentation of non-conformances and corrective actions demonstrates an organization’s commitment to quality, which is essential for obtaining and maintaining certifications such as ISO 13485 for medical devices or GMP for pharmaceuticals. This adherence to standards not only ensures compliance but also enhances the organization’s reputation in the market.
Automation and Efficiency in Non Conformance CAPA Processes
Streamlining CAPA Workflows with Automation
Automation revolutionizes the Non Conformance CAPA process by streamlining workflows and reducing manual intervention. Automated systems can trigger CAPA actions based on predefined criteria, ensuring timely responses to non-conformances. This is particularly beneficial in high-volume manufacturing environments, where manual tracking can be cumbersome and error-prone.
Reducing Human Errors and Enhancing Accuracy
Automated CAPA systems minimize the risk of human errors, enhancing the accuracy and reliability of non-conformance reporting and analysis. By standardizing processes and ensuring consistent data entry, automation contributes to more effective corrective and preventive actions. In the pharmaceutical industry, where precision is critical, automation ensures that CAPA in Pharmaceutical Industry processes are executed flawlessly.
Case Studies: Successful Implementation of Non Conformance CAPA in Life Sciences and Manufacturing
Transforming Quality Management in the Pharmaceutical Industry
A leading pharmaceutical company implemented an advanced Non Conformance CAPA system integrated with their QMS platform. By leveraging data analytics and automation, they reduced the time to resolve non-conformances by 40%, enhanced compliance with regulatory standards, and significantly improved product quality. This transformation not only streamlined their quality management processes but also provided a competitive edge in the market.
Enhancing Product Reliability in Medical Device Manufacturing
A medical device manufacturer adopted a comprehensive Non Conformance CAPA approach to address recurring product defects. By integrating CAPA processes with their PLM system and utilizing root cause analysis tools, they identified and eliminated key issues in their production line. This led to a 30% reduction in product recalls and strengthened their reputation for reliability and quality in the healthcare sector.
Future Trends in Non Conformance CAPA Reporting and Analysis
Embracing Artificial Intelligence and Machine Learning
The future of Non Conformance CAPA lies in the integration of artificial intelligence (AI) and machine learning (ML). These technologies can enhance data analysis, predict potential non-conformances, and recommend optimal corrective actions. CAPA medical device and other high-stakes industries, AI-driven CAPA systems will provide unprecedented levels of precision and efficiency.
Enhancing Real-Time Monitoring and Reporting
Advancements in real-time monitoring technologies will revolutionize CAPA reporting and analysis. IoT devices and sensors can provide continuous data streams, enabling instant detection of non-conformances and prompt corrective actions. This real-time capability is crucial for industries like manufacturing and pharmaceuticals, where immediate responses can prevent widespread issues and maintain high standards of quality.
The Role of ComplianceQuest in Optimizing Non Conformance CAPA Processes
Comprehensive Integration with Quality Management Systems
ComplianceQuest offers a robust platform that seamlessly integrates Non Conformance CAPA with existing Quality Management Systems (QMS) and Product Lifecycle Management (PLM) tools. This comprehensive integration ensures that all aspects of quality management are interconnected, providing a unified approach to handling non-conformances.
Advanced Analytics and Reporting Capabilities
With ComplianceQuest, organizations can leverage advanced analytics and reporting features to gain deeper insights into their CAPA processes. The platform’s intuitive dashboards and real-time data visualization tools empower quality managers to make informed decisions and drive continuous improvement across their operations.
Conclusion
As industries continue to evolve and regulatory landscapes become more complex, the need for advanced quality management systems becomes increasingly critical. ComplianceQuest stands out as an essential tool for businesses in 2025, offering unparalleled integration, automation, and analytical capabilities. By leveraging ComplianceQuest, organizations can effectively manage Non Conformance CAPA processes, ensuring compliance, enhancing product quality, and fostering a culture of continuous improvement. In a competitive and highly regulated environment, ComplianceQuest provides the strategic advantage needed to stay ahead, ensuring that businesses not only meet but exceed quality standards and customer expectations.